El control de l’atmosfera durant el procés de sinterització de l’acer sinteritzat i el seu rendiment
Ambient sinteritzador i la seva selecció
Si només es té en compte la sinterització de l’acer que conté carboni, l’atmosfera de sinterització que s’utilitza a la indústria metal·lúrgica de la pols és l’hidrogen, el nitrogen, el nitrogen + l’hidrogen (potencial de carboni o sense potencial de carboni), la descomposició d’amoníac, gas endotèrmic, gas endotèrmic + nitrogen, síntesi Per al gas i el buit, la selecció correcta de l’atmosfera de sinterització requereix una comprensió de les característiques i el rendiment de diverses atmosferes de sinterització i una selecció d’acord amb els principis de garantir la qualitat i reduir els costos.
L’hidrogen és una atmosfera reductora forta. Molta gent creu que l’hidrogen té un cert efecte de descarburació, però això depèn en gran mesura de la puresa de l’hidrogen utilitzat en lloc del mateix hidrogen. En general, l'hidrogen després de l'electròlisi o la conversió catalítica conté una certa quantitat de gasos d'impuresa, com ara H2O, O2, CO i CH4, etc., de vegades la quantitat total pot arribar al 0.5%. Per tant, és millor assecar-lo i purificar-lo abans d’utilitzar-lo per reduir el contingut d’oxigen i el punt de rosada. No obstant això, a causa de l’alt preu de l’hidrogen, l’hidrogen pur poques vegades s’utilitza com a atmosfera de sinterització tret que hi hagi motius especials.
El nitrogen és un gas inert segur i barat, però, com que el nitrogen pur no té reducció a la temperatura de sinterització, el nitrogen pur rarament s’utilitza com a atmosfera de sinterització en la producció d’acer tradicional de la metal·lúrgia de la pols. En els darrers anys, a mesura que s’ha reduït el cost de la purificació del nitrogen i s’ha millorat la hermeticitat del forn de sinterització, el nitrogen també s’ha començat a utilitzar com a atmosfera de sinterització per a la sinterització d’acer que conté carboni.
En els darrers anys, la barreja de nitrogen-hidrogen s’ha utilitzat cada vegada més en la sinterització de l’acer al carboni. Normalment s’utilitza nitrogen / hidrogen entre 95 / 5-50 / 50. Aquesta barreja té un cert grau de reducibilitat i el punt de rosada pot arribar a ser inferior a -60 ℃, en general, s’ha d’afegir una certa quantitat de CH4 o C3H8 per mantenir un cert potencial de carboni quan s’utilitza aquest gas a 1050-1150 ℃, mentre es sinteritza l’acer al carboni superior a 1250 ℃ no necessita controlar el potencial de carboni. Aquesta barreja es pot utilitzar per sinteritzar aliatges a base de ferro que contenen crom per sota de 1120 ° C sense oxidació.
L’amoníac descompost es produeix descomponent el gas amoníac mitjançant un catalitzador escalfat, inclòs el 75% d’H2 i el 25% de N2. Però, en termes generals, una petita quantitat de molècules d'amoníac no descompostes sempre romanen a l'amoníac descompost. Quan estan en contacte amb metall calent a altes temperatures, es descomponen en àtoms d’hidrogen i nitrogen molt actius, nitrurant així el metall. Estudis recents han demostrat que, si es controla adequadament, la sinterització d'AstaloyCrM a 1120 ° C descompondrà i amoniarà la barreja 90N2 / 10H2 amb una reducció més forta. La raó principal és que aquests àtoms d’hidrogen actius que s’acaben de descompondre durant el procés de sinterització són més eficaços que 90N2 / L’hidrogen del gas mixt 10H2 té una reducció més forta i pot reduir eficaçment la capa d’òxid fora de les partícules AstaloyCrM. Per purificar i descompondre l'amoníac, podeu passar-lo per aigua i assecar-lo, o bé fer servir alúmina activada o tamís molecular per eliminar la resta de l'amoníac que s'elimina.
El gas endotèrmic és un tipus de gas barrejat que s’obté barrejant gas hidrocarbonat (CH4 o C3H8) amb aire en una proporció determinada, preescalfant a 900-1000 ° C i convertint-se catalitzant mitjançant un catalitzador d’òxid de níquel. Depenent de la relació aire-gas de carbó, el procés de conversió s’acompanya de reaccions endotèrmiques o exotèrmiques. El gas mixt resultant s’anomena gas endotèrmic o gas exotèrmic, i la reacció pot ser la següent:
CmHn+m(O2+3.774N2)—mCO+n/H2+1.887mN2
Si la reacció anterior s’ha de dur a terme completament, és a dir, tot el C en CmHm acaba de reaccionar amb O2 a l’aire, l’aire / gas necessari ha de ser m / 2 (1 + 3.774), que és de 2.387m. Per exemple, si el gas hidrocarbonat utilitzat és CH4, l'aire / gas necessari hauria de ser de 2.387 i el gas mixt produït en aquest moment inclou un 40.9% H2, un 38.6% N2 i un 20.5% CO. Després de la reacció, el gas mixt conté H2 El contingut de CO i CO disminueix amb l’augment d’aire / gas, però augmenta el contingut d’H2O i CO2. També mostra que el potencial de carboni del gas barrejat després de la reacció disminueix amb l'augment d'aire / gas i augmenta el rendiment d'oxidació. Aquesta és també la raó principal per la qual poques vegades s’utilitza gas exotèrmic quan es sinteritza acer que conté carboni i s’utilitza la majoria de gas endotèrmic.
En termes generals, el gas mixt produït per l’aire / gas entre 2.0-3.0 s’anomena gas calent d’absorció i el gas mixt produït quan la proporció és superior a 5.0 s’anomena gas exotèrmic. La relació entre el punt de rosada del gas endotèrmic produït amb CH4 com a matèria primera i l’aire / gas mostra que l’aire / gas només augmenta de 2.4 a 2.5 i el punt de rosada del gas mixt produït puja de -25 ° C a superior a 0 ° C. Per tant, si els usuaris produeixen gas endotèrmic per si mateixos, haurien de prestar especial atenció a controlar la proporció d’aire / gas de les matèries primeres (preferiblement no més de 2.4) per obtenir gas endotèrmic amb un punt de rosada prou baix. En el gas barrejat després de la reacció, la proporció dels diferents gasos correspon a la relació al final de la reacció, que és generalment (1000-1100 ° C).
Després de la reacció, si canvia la temperatura del gas, canviarà el potencial de carboni del gas barrejat, el punt de rosada i la proporció de diferents gasos. Molts fabricants de metal·lúrgia de pols utilitzen un generador de gas exotèrmic per subministrar l'atmosfera de sinterització necessària per a diversos forns de sinterització al mateix temps a través de la canonada. La temperatura de l'atmosfera s'ha reduït abans d'arribar al forn de sinterització. . Si l’aïllament de la canonada no és bo i la temperatura de la paret de la canonada és inferior a 800 ° C, llavors una part del carboni del gas mixt es dipositarà a la paret de la canonada en forma de negre de fum. En altres paraules, quan el gas barrejat es reescalfa a la temperatura de sinterització del forn de sinterització, la seva calor de carboni és molt inferior al potencial de carboni que pot proporcionar el generador de gas endotèrmic.
En aquest cas, s’hauria d’afegir una quantitat adequada de metà o propà al forn de sinterització per garantir el potencial de carboni al forn. Ara alguns fabricants estrangers de metal·lúrgia de pols han començat a instal·lar un petit generador de gas endotèrmic al costat de cada forn de sinterització i a utilitzar el gas endotèrmic que s’acaba de produir directament al forn de sinterització sense refredar-se, per evitar afectar l’atmosfera de sinterització a causa dels canvis de temperatura. . . Un altre punt que cal recordar és que, fins i tot amb l’efecte catalític del catalitzador d’òxid de níquel, queda una petita quantitat de gas hidrocarbonat (CH4 o C3H8, etc.) en el gas mixt obtingut després del transport. A més, entre els gasos a 900-1100 ℃ Després que la reacció assoleixi l’equilibri, es produirà una petita quantitat de CO2 i H2O (gasós), que cal assecar abans d’utilitzar-los.
L’addició de nitrogen al gas endotèrmic pot reduir el contingut relatiu de CO, CO2 i H2O al gas endotèrmic, de manera que es amortitzi la sensibilitat de l’atmosfera al potencial de carboni i al punt de rosada, i faci més fàcils alguns coeficients de correlació a l’atmosfera de sinterització. per controlar.
El gas sintètic és un mètode proposat pels fabricants de forns de sinterització estrangers en els darrers anys per generar (diluir) gas endotèrmic directament al forn de sinterització (sense la necessitat d’un generador de gas endotèrmic fora del forn). Barreja alcohol metílic gasós i nitrogen en una proporció determinada i després el passa directament al forn de sinterització. Les reaccions següents es produiran a la zona de sinterització a alta temperatura:
CH3OH — CO + 2H2
Com que la proporció de CO i H2 del gas descompost és igual a la proporció del gas endotèrmic produït pel mètode habitual amb CH4, i el nitrogen mixt es pot combinar per sintetitzar una atmosfera mixta amb la mateixa composició que el gas endotèrmic (1 L El metà correspon a 1.05 nm3 de nitrogen). El seu major avantatge és que no requereix un generador de gas endotèrmic fora del forn. A més, els usuaris poden barrejar diferents quantitats de nitrogen nitrogen per produir gas endotèrmic diluït segons els seus propis requisits.
El buit també és una mena d’atmosfera de sinterització, que s’utilitza principalment per a la sinterització d’acer inoxidable i altres materials, però no s’utilitza habitualment per a la sinterització d’acer al carboni.
Propietats físiques de l'atmosfera sinteritzada
La majoria dels documents i informes de l’atmosfera de sinterització discuteixen principalment sobre el comportament químic entre diferents atmosferes de sinterització i el cos sinteritzat durant el procés de sinterització, però poques vegades discuteixen la influència de les propietats físiques de les diferents atmosferes sobre la sinterització, tot i que aquest efecte no és en molts casos. ser ignorat. Per exemple, la diferència de viscositat dels gasos farà que el gradient de concentració química del cos sinteritzat des de la superfície cap a l'interior al llarg de l'obertura afecti les propietats superficials del cos sinteritzat. Per un altre exemple, la capacitat tèrmica i la conductivitat tèrmica de diferents gasos influeixen molt en el temps de sinterització i la velocitat de refredament. En aquesta secció s'enumeren les principals propietats físiques d'algunes atmosferes de sinterització a diferents temperatures (al voltant de la temperatura de sinterització) per a referència dels lectors.
Exemples de problemes relacionats amb l’atmosfera durant la sinterització
1 Exemples de fissures a la superfície de les parts durant la depilació
Quan s'utilitza un forn de sinterització de cinturó de malla i s'utilitza gas endotèrmic com a atmosfera de sinterització, si la taxa d'augment de temperatura i l'atmosfera a la zona de depilació no es controlen bé, es produirà esquerdes superficials. Molta gent pensa que aquest fenomen es deu a la ràpida descomposició del lubricant. Es produeix, però no és així. La veritable raó és que el monòxid de carboni del gas endotèrmic es descompon en carboni sòlid i diòxid de carboni en el rang de temperatura de 450-700 ℃ sota la catàlisi del ferro, el níquel i altres metalls. És el carboni sòlid recentment dipositat als porus del cos sinteritzat que expandeix el seu volum i provoca l’esmentat fenomen de fissuració superficial.
La qualitat de les peces varia amb la temperatura durant el procés de sinterització en diferents atmosferes. Entre elles, l’atmosfera 3 és gas carbó endotèrmic sec i les atmosferes 4 i 5 són gas carbó endotèrmic afegit amb diferents quantitats de vapor d’aigua. Es pot veure que durant el procés de sinterització, la qualitat de les peces comença a disminuir a uns 200 ° C, cosa que significa que el lubricant sòlid que hi ha dins es descomposa contínuament i desborda el cos de sinterització, reduint-ne la qualitat. Per descomptat, si no hi ha lubricant sòlid a la pols mixta, el fenomen anterior no existeix. Si s’utilitzen les tres atmosferes anteriors, com més seca sigui l’atmosfera de la qualitat del cos sinteritzat a uns 450 ° C, més greu serà aquest fenomen.
Però el que és interessant és que quan s’utilitza el gas 3 (gas endotèrmic sec), es produeixen esquerdes superficials independentment de la presència de lubricants sòlids, cosa que indica que no està directament relacionat amb la depilació i que a les esquerdes es troba gas ric en carboni. Fenomen, podem afirmar la correcció de l’explicació anterior.
Hi ha diverses maneres d'evitar l'aparició del fenomen d'esquerdes esmentat anteriorment. El més directe és canviar l’atmosfera de sinterització de gas endotèrmic a mescla d’hidrogen-nitrogen sense trencar línies trencades. Si no es pot canviar l'atmosfera de sinterització, hi ha dos mètodes. Una d’elles és bufar part del gas endotèrmic que conté vapor d’aigua a la zona de depilació del forn de sinterització. No obstant això, aquest mètode és difícil d'obtenir un control estable en el funcionament real.
El control del flux d’aire del forn de sinterització no és bo i el fenomen de l’atmosfera amb un punt de rosada elevat que entra a la zona de sinterització pot afectar la qualitat de la sinterització. El segon i millor mètode és augmentar la velocitat d’escalfament de les peces a la zona de depilació del forn de sinterització per fer-lo passar 450 el més aviat possible. A la zona on es produeix l’esquerda a -600 ° C, l’anomenada depilació ràpida sol dissenyar-se per a aquest fenomen.
2 Exemple de sinterització AstaloyCrM
El metall crom s'utilitza àmpliament en acers d'aliatge a causa del seu baix preu i el seu bon efecte de reforç. No obstant això, l’acer sinteritzat que conté crom tindrà molts problemes en el seu procés de producció. Una d’elles és la producció de pols de ferro que conté crom, que ha de sotmetre’s a un estricte procés d’atomització i reducció del recuit per obtenir pols de matèria primera amb menor contingut d’oxigen i carboni. .
Honganas AB de Suècia és actualment l'únic fabricant del món que pot produir aquesta matèria primera en pols a baix cost. La segona és que, fins i tot si es pot obtenir pols de ferro que conté crom d’alta qualitat, si la sinterització i la temperatura mitjana, especialment l’atmosfera de sinterització, no es poden controlar bé, serà més probable que s’oxidi durant la sinterització i l’oxidació. es reduirà el rendiment de la sinterització.
Els càlculs termodinàmics i un gran nombre d’experiments han demostrat que si s’utilitza el gas endotèrmic com a atmosfera de sinterització d’AsaloyCrM, els requisits de sinterització no es poden complir encara que el punt de rosada sigui molt baix.
En altres paraules, només es pot utilitzar hidrogen pur o barreja d’hidrogen-nitrogen per a la sinterització d’AsaloyCrM. Actualment, s’utilitzen la majoria d’aquestes últimes. , La proporció d'hidrogen representa un 5% -20%. S'ha de recordar al lector no només per assegurar la composició de l'atmosfera de sinterització, sinó també per garantir la qualitat de l'atmosfera de sinterització.
L'anomenada qualitat aquí es refereix al grau d'oxidació a l'atmosfera de sinterització, que generalment es calibra mitjançant la pressió parcial d'oxigen a l'atmosfera. En sinteritzar a 1120 ℃, si la pressió parcial d’oxigen a l’atmosfera és inferior a 1 × 10-14Pa, no es produirà oxidació durant el procés de sinterització.
Quan es baixa la temperatura, per tal d’evitar l’oxidació, cal que la pressió parcial d’oxigen a l’atmosfera sigui fins i tot baixa. També es pot garantir que l’AsaloyCrM sinteritzat a 1125 ℃ no s’oxidi a 1 × 10-14Pa. El càlcul anterior s’ha confirmat mitjançant dades experimentals.
Conserveu la font i l'adreça d'aquest article per tornar a imprimir-les: El control de l’atmosfera durant el procés de sinterització de l’acer sinteritzat i el seu rendiment
Minghe Empresa de fosa a pressió es dediquen a la fabricació i proporcionen peces de fosa de qualitat i alt rendiment (la gamma de peces de fosa a pressió metàl·lica inclou principalment Fosa a pressió de paret prima,Fundició a càmera calenta,Fosa a pressió a càmera freda), Servei rodó (Servei de fosa a pressió,Mecanitzat en cnc,Fabricació de motllesQualsevol requisit personalitzat de fosa a pressió d’alumini, fosa a pressió de magnesi o de Zamak / zinc i altres foses es pot posar en contacte amb nosaltres.
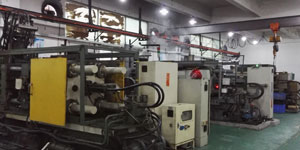
Sota el control d’ISO9001 i TS 16949, tots els processos es duen a terme a través de centenars de màquines avançades de fosa a pressió, màquines de 5 eixos i altres instal·lacions, que van des de les bombes a les rentadores Ultra Sonic. equip d’enginyers, operadors i inspectors experimentats per fer realitat el disseny del client.
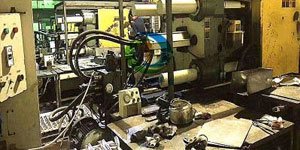
Fabricant contractual de peces de fosa a pressió. Les capacitats inclouen peces de fosa a pressió d’alumini de cambra freda des de 0.15 lliures. fins a 6 lliures, configuració de canvis ràpids i mecanitzat. Els serveis de valor afegit inclouen polit, vibració, desbarbat, granallat, pintura, revestiment, recobriment, muntatge i eines. Els materials treballats inclouen aliatges com 360, 380, 383 i 413.
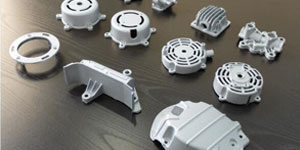
Assistència al disseny de fosa a pressió de zinc / serveis d'enginyeria simultània Fabricant a mida de peces de fosa a pressió de zinc. Es poden fabricar peces de fosa en miniatura, peces de fosa a pressió a alta pressió, peces de motlle multi-lliscant, peces de motlle convencionals, peces de matrius unitats i peces de fosa independents i peces de fosa segellades a cavitat. Les peces de fosa es poden fabricar en longituds i amplades de fins a 24/0.0005 polzades +/- XNUMX polzades de tolerància.
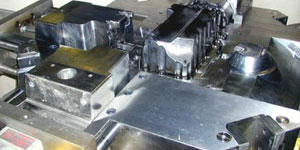
Fabricant certificat ISO 9001: 2015 de magnesi fos a pressió, les capacitats inclouen fosa a pressió de magnesi a alta pressió de fins a 200 tones de càmera calenta i 3000 tones de càmera freda, disseny d’eines, polit, emmotllament, mecanitzat, pintura en pols i líquid, QA complet amb capacitats CMM , muntatge, embalatge i lliurament.
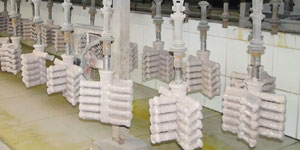
Certificat ITAF16949. Inclou un servei de càsting addicional càsting d'inversió,colada de sorra,Fundició Gravity, Colada d'escuma perduda,Fundició centrífuga,Fundició al buit,Fundició permanent de motllesLes capacitats inclouen EDI, assistència en enginyeria, modelatge sòlid i processament secundari.
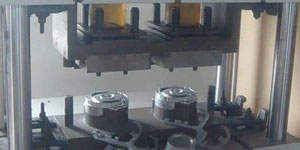
Indústries de fosa Estudis de casos de peces per a: Cotxes, Bicicletes, Avions, Instruments musicals, Embarcacions, Dispositius òptics, Sensors, Models, Dispositius electrònics, Tancaments, Rellotges, Maquinària, Motors, Mobles, Joieria, Plantilles, Telecom, Il·luminació, Dispositius mèdics, Dispositius fotogràfics, Robots, escultures, equip de so, equipament esportiu, eines, joguines i molt més.
Què us podem ajudar a fer a continuació?
∇ Aneu a la pàgina d'inici de Fundició a la Xina
→Peces de fosa-Esbrineu què hem fet.
→ Consells relacionats sobre Serveis de fosa a pressió
By Fabricant de fosa a pressió Minghe | Categories: Articles útils |material etiquetes: Fosa d'alumini, Fosa de zinc, Fosa de magnesi, Fundició de titani, Fundició d'acer inoxidable, Fosa de llautó,Fosa de bronze,Emetent vídeo,Història de l'empresa,Colada de fosa d'alumini | Comentaris desactivats