La pràctica de producció per reduir el consum d'energia
El consum d’energia és el segon consum d’energia després del consum de combustible sòlid en el procés de sinterització, que representa aproximadament un 13% a un 20%. Per tant, reduir el consum d’energia també és una mesura important per reduir el consum d’energia en el procés de sinterització.
1. Reduïu la taxa de fuites d'aire de l'equip i reduïu el consum d'energia
El consum d'energia del ventilador principal d'escapament representa la major part del consum d'energia total de la planta de sinterització. Reduir la taxa de fuites d’aire del sistema de ventilació i augmentar el volum d’aire efectiu a través de la capa de material és de gran importància per estalviar el consum d’energia.
La fuga d’aire entre el carro de sinterització i la caixa de vent (placa de segellat), el carro i el portaobjectes, i el carro i el carro representen més del 80% de la fuga d’aire total de la màquina de sinterització. Per tant, es millora la forma de segellat entre el carro i el portaobjectes, en particular, l’estructura segellada al final de les caixes d’aire del cap i de la cua pot reduir significativament les fuites nocives d’aire, augmentar el flux d’aire efectiu a través de la capa de material, augmentar la producció de sinterització i estalvieu electricitat. A més, la substitució i el manteniment oportuns del carretó, la millora del mètode de tela i la reducció de les fuites d’aire a la vora entre el deflector del carro i la barreja poden reduir eficaçment les fuites nocives d’aire. En reforçar la lubricació, manteniment i gestió de l’equip, es redueix significativament la taxa de fuites d’aire de la màquina de sinterització, s’incrementa molt el flux d’aire efectiu a través de la capa de material, es millora la qualitat del mineral sinteritzat i el consum d’energia. reduït.
Actualment, la major part del segellat del carretó i la corredissa adopta un dispositiu de segellat de placa flotant amb molla instal·lat a la ranura de segellat del carretó. Però l’estructura és defectuosa. El dispositiu de segellat de la corredissa elàstica consisteix principalment a instal·lar una molla en espiral i una placa flotant a la ranura de segellat. Problemes amb aquest tipus de dispositiu de segellat:
Una d’elles és que la mida del tauler flotant no és fàcil de determinar, ja sigui gran o petit, i no només és correcta; el segon és l'envelliment de la molla helicoïdal i perd la seva elasticitat; el tercer és l'acumulació de pols a l'espai de la ranura on es col·loca la molla. Sota el fregament del flux d’aire d’alta velocitat que entrava partícules de pols, els dos extrems de la molla de fulla es van desgastar ràpidament i no es van poder utilitzar durant tres a cinc mesos. A més de les deficiències esmentades anteriorment, els tres tipus de dispositius de segellat esmentats entre el carretó i la corredissa tenen un defecte comú, és a dir, la bretxa entre els dos extrems de la placa flotant i la paret lateral de la ranura de segellat és fàcil de caure a les escòries i a la placa flotant S'enganxa de manera que no pugui flotar cap amunt i cap avall, cosa que provocarà fuites d'aire a la bretxa entre el tauler flotant i la corredissa fixa.
Per tant, per tal de reduir la velocitat de filtració d’aire de sinterització, cal millorar els dispositius de segellat existents que s’han adoptat i inspeccionar regularment el carretó i substituir la placa flotant elàstica flotant. Per millorar efectivament l’efecte de segellat, en una paraula, es poden segellar completament tots els buits de fuites d’aire per reduir la taxa de fuites d’aire de sinterització. En cas contrari, reduir la taxa de filtració d’aire de sinterització només és una conversa buida.
2. Milloreu la permeabilitat a l’aire de la barreja
La resistència de la xarxa de canonades del ventilador de sinterització es compon de dues parts: la pèrdua de pressió de la capa de material sinteritzat i la pèrdua de muntatge de la canonada. La millora de la permeabilitat a l’aire de la capa de material sinteritzat és la clau per reduir la resistència de la xarxa de tubs del ventilador i reduir el consum d’energia. La permeabilitat a l'aire de la capa de material es pot expressar mitjançant la següent fórmula:
- K = Q / A × (h / P) n
- K: transpirabilitat
- Q: volum d'aire que travessa la capa de material m3 / min
- A: superfície de la capa de material m2
- h — Gruix de la capa de material mm
- P: pèrdua de resistència de la capa de material Pa
- n — índex 0.6
Els estudis han demostrat que la mida de les partícules de la barreja sinteritzada té una relació positiva amb la permeabilitat a l’aire, és a dir, la permeabilitat a l’aire de la capa de material augmenta amb l’augment de la mida de les partícules. Per tant, en la producció, afegint una quantitat adequada de calç viva, s’estabilitza la proporció de mineral que retorna, s’incrementa la temperatura de l’aigua calenta de la primera barreja i es preescalfa la segona barreja amb vapor.
(1) Afegiu la quantitat adequada de calç viva
Segons la fórmula de reacció de CaO + H2O = Ca (OH) 2 + 64883KJ / Kg, es pot calcular aproximadament que la temperatura del material sinteritzat de 100 kg es pot augmentar en 39 ° C. En realitat, la temperatura del material augmenta entre 8 ° C i 10 ° C a causa de la pèrdua de calor durant el transport. Teòricament, la proporció de calç viva al 4% pot satisfer el requisit de temperatura del punt de rosada. Tenint en compte la pèrdua de calor, la proporció de calç viva en la producció és del 5%.
(2) Augmenteu la temperatura de la primera aigua calenta barrejada
La temperatura de l'aigua polvoritzada d'un mesclador és superior a 60 ℃, cosa que pot augmentar la temperatura de la mescla i afavorir la digestió de la calç viva.
(3) La segona barreja utilitza vapor per preescalfar
Passar vapor al mesclador secundari també és una mesura per augmentar la temperatura del material. La pràctica ha demostrat que l’ús de vapor pot augmentar la temperatura del material fins a 65 ℃, però quan la producció té un llarg període d’aturada, s’ha de confirmar que la vàlvula de vapor està tancada per evitar que el vapor entri al rodet, provocant una producció innecessària. accidents.
La temperatura de la barreja és la que es mostra a la taula 1:
Taula 1 Temperatura mensual de la barreja
mes | 4 | 5 | 6 | 7 | 8 | 9 |
Temperatura del material ℃ | 55 | 60 | 60 | 62 | 63 | 55 |
(4) Taxa de retorn estable
- ① La quantitat de mineral retornat afecta el rendiment de sinterització. Afecten la producció de sinterització, provoquen la formació de minerals desiguals i disminueixen la força de la formació de mineral.
- ②Les substàncies alcalines i C residuals de mineral afecten l’equilibri C de sinterització i el control de mineral R.
- ③La barreja es pot preescalfar per retornar mineral.
- ④El retorn del mineral és propici per a la granulació de la barreja i millora l’eficiència de la sinterització. Massa petit deteriorarà la permeabilitat de la capa de material, i massa gran provocarà que la barreja es fongui fàcilment, uniformitzi l'estructura del mineral sinteritzat i la resistència sigui pitjor.
La mida de partícula de retorn adequada és de 0.5 a 5 mm; la inestabilitat del carboni residual farà que el carboni fix de la sinterització flucturi, afectant el progrés normal del procés de sinterització; una temperatura de retorn elevada és favorable al preescalfament de la barreja, però no és favorable a la formació de boles de la barreja. Per tant, la proporció de mineral de retorn s’ha de situar entre el 32% i el 40% en la producció. Com es mostra a la taula 2:
Taula 2 Proporció de rendibilitat mensual
mes | 4 | 5 | 6 | 7 | 8 | 9 |
Proporció | 35 | 33 | 32 | 35 | 36 | 37 |
3. Reduir la resistència a la sinterització
La temperatura a la zona d’alta temperatura de sinterització és elevada i la fase líquida produïda augmentarà la resistència del flux d’aire. El nivell de temperatura a la zona d’alta temperatura està determinat per la temperatura i el gruix de la zona de combustió, que depèn no només del balanç de calor de la zona de combustió, sinó també de la velocitat de combustió i la velocitat de transferència de calor del carboni sòlid. Per tant, les propietats fisicoquímiques del combustible afecten directament la resistència de la zona de combustió sinteritzada. Té la relació següent:
Quantitat de combustible: augmenta la quantitat de combustible, que no només augmenta la temperatura de la zona de combustió, sinó que també augmenta el seu gruix;
Mida de les partícules de combustible: augmenta la mida de les partícules de combustible. A mesura que la velocitat de combustió disminueix i el temps de combustió s’allarga, disminueix la temperatura de la zona de combustió i augmenta el gruix. Velocitat del flux d’aire: la velocitat del flux d’aire afecta la velocitat de transferència de calor i la velocitat de combustió, però el grau d’influència és diferent. Quan augmenta la velocitat del flux d’aire, la velocitat de transferència de calor i la velocitat de combustió es desenvolupen a velocitats diferents, i la bretxa entre ambdues augmenta gradualment, provocant que la transferència de calor i la combustió es desconnectin, reduint la temperatura de la capa de combustió i augmentant el gruix. En la producció real, s’ha de controlar el flux d’aire de manera que la velocitat de combustió i la velocitat de transferència de calor siguin similars per aconseguir la temperatura de combustió més alta i l’amplada de la zona de combustió més estreta. Per a pols de coc, 1mm ~ 3mm es considera la millor mida de partícula, i la mida de partícula de pols de coc de la segona àrea d'operació de la zona de sinterització Beiying de Benxi Iron and Steel es controla bàsicament al 78% si és inferior a 3mm . Com es mostra a la taula 3:
Taula 2 Proporció de rendibilitat mensual
mes | 4 | 5 | 6 | 7 | 8 | 9 |
% De granularitat | 78 | 79 | 78 | 80 | 79 | 80 |
4. Utilitzeu la regulació de la velocitat de freqüència variable i la compensació del condensador per reduir el consum d'energia
La tecnologia de regulació de velocitat de conversió de freqüència és un mètode de regulació de velocitat segur, fiable i raonable desenvolupat en els darrers anys. Assoleix el propòsit d’ajustar la velocitat del motor convertint el corrent altern amb una determinada tensió i freqüència utilitzades en la producció diària en un corrent altern amb una freqüència i tensió variables a través d’un convertidor. Després que el motor de velocitat variable adopti la regulació de la velocitat de conversió de freqüència, es redueix el corrent mitjà i s’estalvia energia elèctrica. En la producció real, per tal de perseguir la velocitat de funcionament de l’equip, juntament amb la qualitat, el funcionament i altres motius de l’equip, la potència del motor sovint s’incrementa artificialment, cosa que provoca el fenomen del "gran carro tirat per cavalls", que augmenta la potència del motor i malgasta energia elèctrica. . A la segona zona de sinterització de la zona de sinterització Beiying de Benxi Iron and Steel, després d’un any de pràctiques de producció, ha millorat contínuament el seu propi nivell operatiu i la seva experiència acumulada. Ha fet esforços continus per estalviar energia i reduir el consum en sinterització. Durant la producció normal, la potència mitjana dels dos ventiladors principals d’escapament ha canviat de l’original. La qualitat i la quantitat de sinterització es poden reduir a uns 5500Kw / h des d’uns 6000Kw / h a uns 5500Kw / h. Al mateix temps, la qualitat i la quantitat de sinterització compleixen plenament els requisits de producció de l’alt forn.
Observacions finals: L’estalvi d’energia sinteritzador és una tasca difícil i persistent a llarg termini que ha de ser completada pels treballadors sinteritzadors. S’ha d’explorar, resumir, millorar i perfeccionar constantment en la producció. Només sota la premissa del control de qualitat i la reducció de costos podem mantenir-nos ferms en el feble mercat actual de l’acer, de manera que la conservació d’energia i la reducció d’emissions són la tasca de tota la vida dels treballadors de la sinterització.
Conserveu la font i l'adreça d'aquest article per tornar a imprimir-les: La pràctica de producció per reduir el consum d'energia
Minghe Empresa de fosa a pressió es dediquen a la fabricació i proporcionen peces de fosa de qualitat i alt rendiment (la gamma de peces de fosa a pressió metàl·lica inclou principalment Fosa a pressió de paret prima,Fundició a càmera calenta,Fosa a pressió a càmera freda), Servei rodó (Servei de fosa a pressió,Mecanitzat en cnc,Fabricació de motllesQualsevol requisit personalitzat de fosa a pressió d’alumini, fosa a pressió de magnesi o de Zamak / zinc i altres foses es pot posar en contacte amb nosaltres.
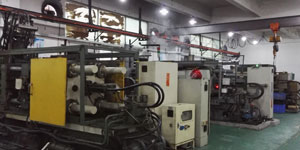
Sota el control d’ISO9001 i TS 16949, tots els processos es duen a terme a través de centenars de màquines avançades de fosa a pressió, màquines de 5 eixos i altres instal·lacions, que van des de les bombes a les rentadores Ultra Sonic. equip d’enginyers, operadors i inspectors experimentats per fer realitat el disseny del client.
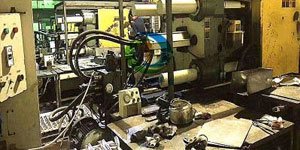
Fabricant contractual de peces de fosa a pressió. Les capacitats inclouen peces de fosa a pressió d’alumini de cambra freda des de 0.15 lliures. fins a 6 lliures, configuració de canvis ràpids i mecanitzat. Els serveis de valor afegit inclouen polit, vibració, desbarbat, granallat, pintura, revestiment, recobriment, muntatge i eines. Els materials treballats inclouen aliatges com 360, 380, 383 i 413.
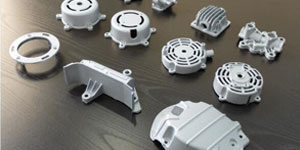
Assistència al disseny de fosa a pressió de zinc / serveis d'enginyeria simultània Fabricant a mida de peces de fosa a pressió de zinc. Es poden fabricar peces de fosa en miniatura, peces de fosa a pressió a alta pressió, peces de motlle multi-lliscant, peces de motlle convencionals, peces de matrius unitats i peces de fosa independents i peces de fosa segellades a cavitat. Les peces de fosa es poden fabricar en longituds i amplades de fins a 24/0.0005 polzades +/- XNUMX polzades de tolerància.
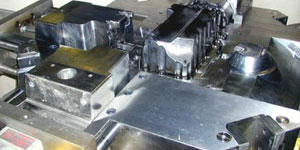
Fabricant certificat ISO 9001: 2015 de magnesi fos a pressió, les capacitats inclouen fosa a pressió de magnesi a alta pressió de fins a 200 tones de càmera calenta i 3000 tones de càmera freda, disseny d’eines, polit, emmotllament, mecanitzat, pintura en pols i líquid, QA complet amb capacitats CMM , muntatge, embalatge i lliurament.
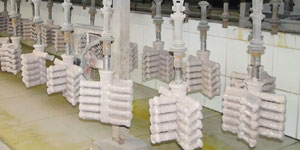
Certificat ITAF16949. Inclou un servei de càsting addicional càsting d'inversió,colada de sorra,Fundició Gravity, Colada d'escuma perduda,Fundició centrífuga,Fundició al buit,Fundició permanent de motllesLes capacitats inclouen EDI, assistència en enginyeria, modelatge sòlid i processament secundari.
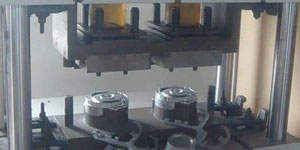
Indústries de fosa Estudis de casos de peces per a: Cotxes, Bicicletes, Avions, Instruments musicals, Embarcacions, Dispositius òptics, Sensors, Models, Dispositius electrònics, Tancaments, Rellotges, Maquinària, Motors, Mobles, Joieria, Plantilles, Telecom, Il·luminació, Dispositius mèdics, Dispositius fotogràfics, Robots, escultures, equip de so, equipament esportiu, eines, joguines i molt més.
Què us podem ajudar a fer a continuació?
∇ Aneu a la pàgina d'inici de Fundició a la Xina
→Peces de fosa-Esbrineu què hem fet.
→ Consells relacionats sobre Serveis de fosa a pressió
By Fabricant de fosa a pressió Minghe | Categories: Articles útils |material etiquetes: Fosa d'alumini, Fosa de zinc, Fosa de magnesi, Fundició de titani, Fundició d'acer inoxidable, Fosa de llautó,Fosa de bronze,Emetent vídeo,Història de l'empresa,Colada de fosa d'alumini | Comentaris desactivats