Recollida de defectes comuns i mesures preventives en carburació i atenuació
La carburació i apagat és en realitat un procés compost, és a dir, carburació + apagat. Sovint s’acostuma a parlar dels dos junts, perquè els dos processos que s’acaben amb el mateix equip són els més freqüents en la producció (però també hi ha refrigeració per aire de carburació, carburació de refrigeració lenta i després processos de reescalfament i apagat, i processos secundaris Procés) Aleshores, alguns dels fenòmens indesitjables que es produeixen en la producció són problemes de carburació, d’altres són problemes de sufocació i d’altres són el resultat dels efectes combinats de la carburació i la temptació.
Sabem que tots els processos de tractament tèrmic són inseparables de tres qüestions bàsiques: calefacció, conservació de calor i refrigeració. En detall, incloent la temperatura d’escalfament, la velocitat d’escalfament, el temps de retenció, la velocitat de refrigeració i, per descomptat, els problemes d’atmosfera. Així, doncs, quan alguna cosa no funciona, analitzarem habitualment la causa a partir d’aquests aspectes.
Per a la carburació i apagat, sovint provem aquests indicadors: aspecte de la superfície del producte, duresa superficial, duresa del nucli, profunditat de la capa carburada, (profunditat efectiva de la capa endurida, profunditat de la capa totalment endurida) estructura metalogràfica i deformació. Compartim la meva opinió sobre aquests indicadors respectivament.
1. Problema d'aparença
1. Escala d'òxid: es deu principalment a la fuita d'equips, al gas portador impur o al contingut d'aigua. Necessiteu trobar el motiu dels equips i les matèries primeres.
2. L'altre problema més problemàtic és el problema de les taques, que també és un requisit nou i desafiant per al tractament tèrmic en l'època moderna. Els motius són complicats i molt profunds.
dos. Duresa no qualificada
1. Elevada duresa (no discutida)
2. Baixa duresa: hi ha dues situacions, una és la carburació sense qualificar. El motiu pot ser que la capa carburada és massa superficial per satisfer els requisits dels dibuixos (la capa carburada no està infiltrada) o que l’escala de detecció seleccionada supera l’interval tolerable de la capa carburada existent, que trencarà la capa carburada.
Solució: reposeu les filtracions i seguiu la regla d’inspecció. JBT 6050-2006 "Principis generals per a la inspecció de la duresa del tractament tèrmic de les peces d'acer" La profunditat de la capa carburada depèn en realitat de la temperatura, el temps i el potencial de carboni. A partir dels factors anteriors, podem considerar maneres d’augmentar la temperatura d’escalfament, allargar el temps de retenció i augmentar el potencial de carburació. (Per descomptat, l'ajust de cada paràmetre s'ha de combinar completament amb els requisits dels vostres propis equips i productes) També pot ser a causa de l'existència d'organitzacions que no són cavalls a la superfície. Una altra situació es produeix quan la duresa és baixa, és a dir, la carburació està qualificada, però l’apagat no està qualificat. En termes generals, no s’apaga. Aquesta situació és la més complicada, com diu la dita: el tractament tèrmic depèn de la calefacció durant tres quarts i la refrigeració durant set quarts. També reflecteix la posició que ocupa el procés de refredament en el procés de tractament tèrmic.
La següent és una prova comparativa que vaig dissenyar. Podeu parlar de l’efecte del refredament sobre la duresa.
Agafeu 3 grups de barres de prova amb materials diferents, però amb les mateixes especificacions i dimensions, la mida de les quals és de mm20mmX100mm. (Anomenem la barra de prova d’acer núm. 20, la barra de prova 1Cr núm. 20 i la barra de prova 2CrMnTi núm. 20). Les barres de prova es carburen a la mateixa calor mitjançant el mateix procés. Suposant que la profunditat de la capa carburada de les tres barres de prova sigui de 3-0.6 mm (ps: la suposició només s’estableix en un estat ideal).
Tingueu en compte les condicions següents:
a. Acabeu d’apagar les mateixes condicions
b. El mitjà d’apagat és oli lent, oli ràpid, aigua clara i aigua salada
c. En el mateix mitjà sense remenar i remenant i apagant intensament, les tres barres de prova es prenen cadascuna en dos grups per provar-les.
Després de completar la carburació, el grup A s’apaga a 800 graus i el grup B s’apaga a 860 graus. Quin és l’ordre de la seva duresa d’alta a baixa? Com ordenar la capa endurida (amb 550HV1.0 com a límit) de profunda a poc profunda? Agafeu dues barres de prova del mateix material i compareu i proveu, quin grup pot obtenir una duresa de tremp superior i una profunditat de capa endurida efectiva?
Es pot concloure a partir dels resultats de la prova anteriors que la profunditat de la capa carburada no és igual a la profunditat de la capa eficaç endurida i que la profunditat real de la capa endurida es veu afectada per l’enduriment del material, la temperatura d’apagat i el refredament taxa. Les característiques de refredament i la intensitat de refredament del medi de refredament també afecten l’efecte de refredament. Les opcions anteriors són opinions de la gent, si hi ha incompletesa, podeu afegir. Per descomptat, l’efecte de mida de les peces també afecta l’efecte d’enduriment.
Crec que un inspector experimentat pot determinar la causa real de la baixa duresa organitzant i combinant altres mètodes de prova, i després trobar la causa real per resoldre-la; com a artesà, si coneixeu les característiques de les matèries primeres metàl·liques convencionals, el rendiment de refrigeració dels seus propis equips i suports ha assolit un cert nivell de reconeixement, cosa que és de gran ajuda per a la formulació de processos de carburació i apagat.
3. Duresa desigual: temperatura uniforme del forn (que afecta la uniformitat de carburació), estructura de l’equip, circulació de l’atmosfera, càrrega del forn (que afecta la uniformitat de la capa de carburació i, alhora, afecta la uniformitat d’apagat)
4. La duresa del nucli no està qualificada. Massa alta: la temperatura d’apagat és massa alta, l’enduriment del material és massa bo, el límit superior de composició de carboni i aliatges i la velocitat de refredament mitjana és massa ràpida. La duresa del nucli és baixa: tot el contrari.
Compartiment d’exemples: producte d’acer 20 # 1.5mm, requisits: capa d’infiltració de 0.2-0.4mm nucli HV250, alguns amics de la mateixa indústria pensen que els requisits no són raonables (tothom hauria de saber que la duresa més alta de la martensita de llosa d’acer 20 HV450- 470) Per resoldre aquest problema, primer hem d’entendre les característiques d’aquest material: incloent l’enduriment i l’enduriment.
A continuació, combineu els factors esmentats anteriorment que afecten l’efecte de sufocació i busqueu maneres d’escalfar i refredar. En aquest cas, el material és fix. Podem esbrinar un camí a partir de la temperatura d’apagat i la velocitat de refredament. Aquest fabricant utilitza oli de velocitat excessiva. Si la reducció de la intensitat d’apagat no compleix els requisits, també podem reduir la temperatura d’apagat. Mètode.
Encara la mateixa frase, de 860-760 graus, (quan la temperatura es redueix a un nivell determinat, una certa quantitat de ferrita precipitarà de l'austenita supercooled al nucli i la duresa disminuirà en aquest moment., Com més la temperatura disminueix, com més precipita la quantitat de ferrita, més disminueix la duresa.
Heus aquí un recordatori: cal combinar completament les condicions existents de l’equip i fer un enrenou sobre l’índex favorable especial de permeabilitat poc profunda.
3. La capa carburada o capa carburada efectiva és més profunda i superficial
Com s’ha esmentat anteriorment, la profunditat de la capa d’infiltració depèn de la temperatura, el temps i la concentració de carboni. Per solucionar aquest problema, hem de començar amb la temperatura d’escalfament, la velocitat d’escalfament, el temps de retenció, la velocitat de refredament i el control del gradient de concentració de carboni a la capa de carboni. Com més alta sigui la temperatura, més temps serà i més gran serà el potencial de carboni, més profunda serà la capa d’infiltració i viceversa.
Però, de fet, és molt més que simple. Per dissenyar un procés de carburació, també heu de tenir en compte l’equip, la capacitat del forn, les característiques de l’oli, l’estructura metalogràfica, l’enduriment del material, el gradient de concentració de carboni a la capa carburada i la velocitat de refredament. I molts altres factors. Això es pot analitzar fent referència a la situació anterior de baixa duresa i no s’explicarà en profunditat.
En quart lloc, organització metal·logràfica
Martensita excessiva: la matèria primera té grans grossos o no està normalitzada i la temperatura de carburació és massa elevada. Solució: normalització o normalització múltiple (es recomana que la temperatura normalitzadora sigui 20-30 graus més alta que la temperatura de carburació) Si és possible, tingueu en compte la carburació i un refredament lent i, a continuació, tornar a escalfar i apagar
Paralímpic excessiu: la temperatura d’apagat és massa alta, el contingut de carboni a l’austenita és massa alt (el potencial de carboni és massa alt). Solució: la difusió completa i les condicions permeten reduir la temperatura d’apagat, el temperat i el reescalfament i apagat a alta temperatura o el tractament criogènic.
Carbur excessiu: contingut de carboni massa alt en austenita (potencial de carboni massa alt), procés de refredament massa lent, precipitació de carbur
Solució: totalment difusa, controleu la velocitat de refredament, reduïu la diferència de temperatura entre carburació i apagat el màxim possible i utilitzeu la temperatura o baixa temperatura el menys possible. Si s’ha d’utilitzar aquest procés, s’ha de controlar la càrrega del forn. Imaginem-nos: el mateix equip es carburitza a 920 ° C i s’apaga a 820 ° C. La capacitat del forn és de 1000 kg i 600 kg i la velocitat de refrigeració és la mateixa? Quin trigarà més? Quin grau de carbur és més alt?
Cincs. Oxidació interna i no equina
Oxidació interna: és la reacció entre elements d’aliatge com el crom, el manganès i el molibdè de l’acer i l’atmosfera oxidant de l’atmosfera (principalment oxigen, aigua, diòxid de carboni), que esgota els elements d’aliatge de la matriu, cosa que provoca una disminució en l’enduriment del material. L’estructura de la xarxa negra es pot veure al microscopi, la seva essència és l’estructura de troostita obtinguda per l’esgotament d’elements d’aliatge a la matriu i la disminució de l’enduriment.
La solució és trobar maneres d’augmentar la velocitat de refredament del medi, augmentar la intensitat d’apagat i reduir l’atmosfera oxidant al forn (assegurar la puresa de les matèries primeres i auxiliars de carburació, minimitzar la quantitat d’aire equilibrat, controlar l’equilibri contingut d’humitat de l’aire i assegureu-vos que l’aparell no fuig. Prou d’escapament) És difícil eliminar els equips convencionals. Es diu que els equips de carburació al buit a baixa pressió es poden eliminar completament. A més, una potent injecció fotogràfica també pot reduir el nivell d’oxidació interna.
He llegit les opinions d'alguns experts, i alguns creuen que l'excés d'amoníac en el procés de carbonitruració també pot causar greus no equivocacions. Personalment tinc una opinió diferent sobre això: potser és causada per un contingut excessiu d’aigua en amoníac? Com que he estat exposat a molts processos de carbonitruració, no es va trobar cap teixit obvi que no fos cavall en inspeccionar el producte. (Però no crec que aquesta visió sigui errònia) Algunes indústries de maquinària estrangeres concedeixen una gran importància a l'oxidació interna, especialment a la indústria d'engranatges. A nivell nacional, la profunditat generalment no ha de ser superior a 0.02 mm segons la qualificació.
No martensític: apareix una estructura no martensítica a la superfície de la capa carburada a causa de problemes de carburació o apagat després de l’apagat, com ferrita, bainita i, per descomptat, troostita tipus oxidació interna. El mecanisme de generació és similar a l’oxidació interna i la solució és similar.
Sis. Problema de deformació
Aquest és un problema del sistema, i també és el problema més molest per al nostre personal dedicat al tractament tèrmic. Es garanteix des de diversos aspectes del medi de refredament del procés de matèria primera. El contingut anterior només és una experiència personal. Si hi ha incoherències, podeu corregir-me, gràcies.
Conserveu la font i l'adreça d'aquest article per tornar a imprimir-les:Recollida de defectes comuns i mesures preventives en carburació i atenuació
Minghe Empresa de fosa a pressió es dediquen a la fabricació i proporcionen peces de fosa de qualitat i alt rendiment (la gamma de peces de fosa a pressió metàl·lica inclou principalment Fosa a pressió de paret prima,Fundició a càmera calenta,Fosa a pressió a càmera freda), Servei rodó (Servei de fosa a pressió,Mecanitzat en cnc,Fabricació de motllesQualsevol requisit personalitzat de fosa a pressió d’alumini, fosa a pressió de magnesi o de Zamak / zinc i altres foses es pot posar en contacte amb nosaltres.
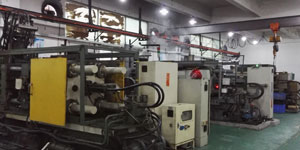
Sota el control d’ISO9001 i TS 16949, tots els processos es duen a terme a través de centenars de màquines avançades de fosa a pressió, màquines de 5 eixos i altres instal·lacions, que van des de les bombes a les rentadores Ultra Sonic. equip d’enginyers, operadors i inspectors experimentats per fer realitat el disseny del client.
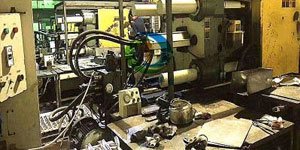
Fabricant contractual de peces de fosa a pressió. Les capacitats inclouen peces de fosa a pressió d’alumini de cambra freda des de 0.15 lliures. fins a 6 lliures, configuració de canvis ràpids i mecanitzat. Els serveis de valor afegit inclouen polit, vibració, desbarbat, granallat, pintura, revestiment, recobriment, muntatge i eines. Els materials treballats inclouen aliatges com 360, 380, 383 i 413.
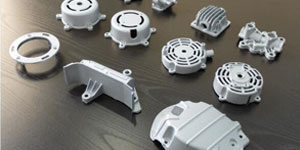
Assistència al disseny de fosa a pressió de zinc / serveis d'enginyeria simultània Fabricant a mida de peces de fosa a pressió de zinc. Es poden fabricar peces de fosa en miniatura, peces de fosa a pressió a alta pressió, peces de motlle multi-lliscant, peces de motlle convencionals, peces de matrius unitats i peces de fosa independents i peces de fosa segellades a cavitat. Les peces de fosa es poden fabricar en longituds i amplades de fins a 24/0.0005 polzades +/- XNUMX polzades de tolerància.
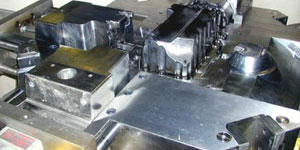
Fabricant certificat ISO 9001: 2015 de magnesi fos a pressió, les capacitats inclouen fosa a pressió de magnesi a alta pressió de fins a 200 tones de càmera calenta i 3000 tones de càmera freda, disseny d’eines, polit, emmotllament, mecanitzat, pintura en pols i líquid, QA complet amb capacitats CMM , muntatge, embalatge i lliurament.
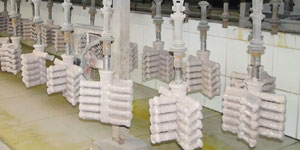
Certificat ITAF16949. Inclou un servei de càsting addicional càsting d'inversió,colada de sorra,Fundició Gravity, Colada d'escuma perduda,Fundició centrífuga,Fundició al buit,Fundició permanent de motllesLes capacitats inclouen EDI, assistència en enginyeria, modelatge sòlid i processament secundari.
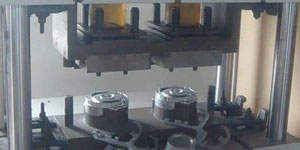
Indústries de fosa Estudis de casos de peces per a: Cotxes, Bicicletes, Avions, Instruments musicals, Embarcacions, Dispositius òptics, Sensors, Models, Dispositius electrònics, Tancaments, Rellotges, Maquinària, Motors, Mobles, Joieria, Plantilles, Telecom, Il·luminació, Dispositius mèdics, Dispositius fotogràfics, Robots, escultures, equip de so, equipament esportiu, eines, joguines i molt més.
Què us podem ajudar a fer a continuació?
∇ Aneu a la pàgina d'inici de Fundició a la Xina
→Peces de fosa-Esbrineu què hem fet.
→ Consells relacionats sobre Serveis de fosa a pressió
By Fabricant de fosa a pressió Minghe | Categories: Articles útils |material etiquetes: Fosa d'alumini, Fosa de zinc, Fosa de magnesi, Fundició de titani, Fundició d'acer inoxidable, Fosa de llautó,Fosa de bronze,Emetent vídeo,Història de l'empresa,Colada de fosa d'alumini | Comentaris desactivats